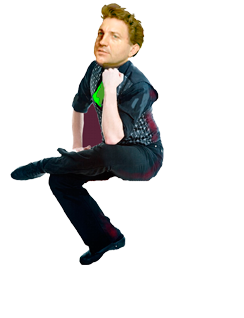
На базе завода «Авангард», который уже 75 лет беспрерывно выпускает электронику для гражданских и военных нужд, в этом году началось производство продукции для «Ростелекома» — от IP-телефонов и видеокамер до коммутаторов и серверов. Как организован процесс, как контролируется качество продукции и какие заказы готово выполнять предприятие, узнали журналисты из регионов Севера-Запада во время пресс-тура «От «железа» до контента».
К запуску новой линии по выпуску продукции начали готовиться еще два года назад. Сначала полностью очистили пространство, разобрав перекрытия, сняв потолки и заменив окна. Ремонт шел около года, за это время помещение площадью 2 тыс. квадратных метров кардинально преобразились: появился зал, где производится и ремонтируется оборудование, зал для сборки устройств, зона упаковки, испытательные лаборатории, склад готовой продукции. При ремонте использовались специальные материалы: например, полы покрыты материалом, который снижает вибрационную нагрузку, а стены — антистатической краской. После этого было установлено самое современное оборудование. Торжественное открытие производства состоялось в июне этого года.
За выпуск продукции отвечает НПО «Российские телекоммуникационные технологии» («РТТ») — совместное предприятие ПАО «Ростелеком», группы компаний «Авангард» и ООО «Кьютек».
— Все мы знаем, что технологическая независимость стала одной из основных задач нашего государства. «Ростелеком» часть этих задач реализует вместе с нами. Поэтому было принято решение организовать здесь производство для того, чтобы под своим надзором, при контроле качества, цены и скорости выпускать продукцию, которую «Ростелеком» использует в своих проектах, — рассказала генеральный директор ООО «НПО РТТ» Ирина Спицына. Когда мы запускались, была задача сделать производство полного цикла — чтобы мы на выходе выдавали коробку с готовой продукцией, которая идет со склада заказчикам по всей географии «Ростелекома».
Ирина Спицына провела экскурсию по производству, которое в тот момент находилось в процессе перенастройки: компания выполнила один крупный заказ, собрав тысячи IP-телефонов, и готовилась к производству другого оборудования — коммутаторов.
Исходные материалы (в профессиональной среде их называют давальческим сырьем) компания получает от заказчика — будь то печатные платы, комплектующие, литые корпуса для техники. И в этом месте все собирается воедино, чтобы в итоге получилось готовое к эксплуатации устройство — запрограммированное и с инструкцией в упаковке. Но в промежутке между двумя этими стадиями происходит довольно сложный процесс.
Основа всего — печатная плата. Перед тем как с ней начнут работать, она маркируется штрих-кодом, в который «вшивается» вся необходимая информация — например, к какому оборудованию она относится, какого числа поступила на производство, кто является заказчиков. Следующий этап — нанесение на плату паяльной пасты. Происходит это через трафарет — капли пасты наносятся на те места, куда позже будут установлены компоненты. Компоненты хранятся в специальных шкафах с низким уровнем влажности (а некоторые — вообще в бескислородной среде).
Компоненты устанавливаются с большой скоростью (максимальная мощность линии составляет 240 тыс. компонентов в час). После этого плата с компонентами попадает в зону технического контроля. Устройство в автоматическом режиме проверяет, насколько корректно были произведены все операции. И если что-то пошло не по плану, то подается сигнал принтеру — добавить или убавить паяльную пасту.
Это первый проверочный этап, а их в «заводской жизни» платы будет несколько. Благодаря таким точкам контроля удается достичь высокого качества продукции и минимизировать количество брака.
В печи установленные на плату компоненты «запекаются». Установленная на предприятии печь — уникальное для российских компаний оборудование, она имеет двенадцачть зон постепенного нагрева (это нужно, чтобы паста не потрескалась) и три зоны охлаждения. Из печи плата попадает в контроллер, который просвечивает ее, чтобы увидеть, где ножки компонентов не припаялись или где неверно встали на плату. Распределитель отделяет качественные платы от тех, которые получились с отклонениями. Если обнаруживаются несоответствия заданным параметрам, то процесс останавливается — необходимо понять, была ли ошибка массовой или это единичный случай.
На следующем этапе происходит установка больших выводных элементов — например, трансформаторов, разъемов, катушек. Занимаются этим уже операторы. Однако в отличие от других производств, здесь элементы припаиваются не вручную, а на оборудовании для селективной пайки. Установка автоматически подъезжает к каждому выводу и припаивает оловом. После этого плата отправляется на последнюю оптическую инспекцию, а затем — в финальный буфер.
Готовые платы на тележке транспортируются в соседний зал — участок автоматизированного монтажа. Это своего рода конвейер, который проходит между столами операторов. Каждый из работников выполняет свою функцию: вставляет плату, закрепляет корпус, подключает провода, программирует. По словам Ирины Спицыной, за счет того, что сотрудник выполняет только определенную манипуляцию, достигается высокая скорость сборки. Если на производстве плат задействованы высококвалифицированные работники и инженеры, за которыми компания буквально «охотится», то к работникам этого участка предъявляются несколько иные требования — они должны быть внимательными и аккуратными.
Отдельно организованы персональные места для инженеров, которые в одиночку могут делать все те же операции, которые делают последовательно операторы на линии. Таких работников задействуют, когда потребуется изготовить небольшую партию какого-либо оборудования.
Потенциальная мощность предприятия — 1 млн изделий в год. Однако все зависит от того, какое именно оборудование надо выпустить в тот или иной промежуток времени. И все упирается в плату: на ней может быть 100 компонентов, а может — несколько тысяч. Тем не менее, уверена Ирина Спицына, предприятие готово полностью закрыть все потребности «Ростелекома» в новом оборудовании с минимальными технологическими потерями. Если появится объемный заказ, то предприятие перейдет на трехсменный режим работы — и оборудование будет задействовано 24 часа в сутки и 7 дней в неделю.
— Мы делаем массовую продукцию, то есть недорогую — такая задача поставлена «Ростелекомом». При этом есть задачи и по собственной компонентной базе — например, дочерняя компания в контуре «Ростелекома» уже занимается дизайном микроконтроллеров и микропроцессоров, — рассказала Ирина Спицына.
Кирилл Наумов
- Слушайте, то, что вы несете, это полная ахинея! Так нельзя! Создается ощущение, что вы против всего, что составляет естественный порядок вещей. Вам доставляет удовольствие издеваться над людьми. Вы анархисты и даже террористы!
Ольга Сырцова, госслужащая